Precision and Excellence: Best Practices for Successful Aluminum Spreading
In the world of aluminum casting, accomplishing accuracy and excellence is not just a goal however a requirement that identifies quality. The meticulous process of aluminum spreading needs focus to information at every stage, from product option to last ending up touches. casting aluminum illinois. Each step along the way adds to the supreme success of the casting procedure, needing a deep understanding of the interaction in between variables such as mold style, process optimization, quality assurance, and finishing methods. As we navigate with the complexities of this craft, revealing the most effective practices that pave the way for flawless aluminum spreadings comes to be a trip worth task.
Material Selection
When considering product option for aluminum spreading procedures, durability, and warmth resistance are critical aspects to evaluate,. Light weight aluminum alloys supply a vast array of choices, each with unique residential or commercial properties that can dramatically impact the high quality and performance of the final casted product. One common option is the 356 alloy, known for its outstanding fluidity and resistance to corrosion, making it ideal for a range of applications. For high-stress settings needing superior strength, the 7075 alloy stands out because of its high strength-to-weight ratio. Furthermore, the 6061 alloy is preferred for its great weldability and formability, making it a functional choice for detailed styles.
In the selection procedure, it is crucial to consider not only the mechanical residential properties of the alloy yet additionally its thermal characteristics. Heat resistance is important to make sure that the casted component can stand up to the temperature levels it will certainly be exposed to during procedure without endangering its architectural honesty. By meticulously reviewing the durability and warmth resistance of various light weight aluminum alloys, suppliers can make enlightened choices that cause high-grade, trusted casted items.
Mold And Mildew Style
In the realm of aluminum spreading finest methods, an integral aspect that significantly affects the end product's quality and honesty is the thorough style of the mold. Mold and mildew style plays a crucial function in identifying the dimensional accuracy, surface area finish, and overall details of the actors aluminum component. When producing a mold for light weight aluminum spreading, a number of key variables need to be thought about to ensure ideal results.
To start with, the mold layout must account for the product circulation characteristics of liquified aluminum to protect against flaws such as shrinkage, porosity, or misruns. Appropriate gating and riser placement are necessary elements in the mold and mildew layout procedure to help with smooth steel circulation and minimize the development of air pockets.
Additionally, the mold layout ought to take into account the cooling rate of the light weight aluminum to avoid fracturing or distortion during solidification. Appropriate venting and cooling networks within the mold and mildew can help manage the temperature distribution and promote consistent solidification of the metal.
Process Optimization
To boost efficiency and quality in aluminum casting, procedure optimization plays a pivotal duty in streamlining procedures and maximizing result. By fine-tuning each step of the spreading process, manufacturers can determine traffic jams, lower waste, and boost overall performance.
Additionally, applying lean production principles can even i loved this more improve process optimization in aluminum spreading. By eliminating non-value-added tasks and focusing on continuous renovation, suppliers can accomplish higher performance degrees and better source use. Furthermore, regular surveillance and analysis of key efficiency indicators (KPIs) aid in determining areas for renovation and making data-driven decisions to maximize the casting procedure continuously.
Quality Assurance
Refine optimization in aluminum spreading not only improves performance and efficiency but likewise lays the foundation for rigid quality assurance actions to promote sector requirements. Quality assurance is critical in making sure that final aluminum spreadings meet the called for specifications and performance standards. Executing a thorough quality control procedure entails different actions, beginning with the initial style stage through to the final assessment of the actors parts.

Additionally, developing clear quality assurance methods and paperwork procedures is necessary for tracking and keeping an eye on the casting procedure. By preserving thorough records of manufacturing parameters, screening results, and assessment reports, makers can ensure uniformity and traceability in their light weight aluminum casting operations. Sticking to rigorous top quality control practices not just enhances the general reliability of aluminum spreadings but also imparts self-confidence in clients pertaining to find more information the quality of the end products.
Finishing Methods
Just how can light weight aluminum casting be improved via meticulous application of completing methods? Ending up techniques play a vital duty in elevating the high quality and appearances of aluminum castings. One of the main techniques used is surface area why not try here smoothing, which involves the removal of any type of blemishes or harsh sides to attain a flawless finish. This process not only improves the visual charm of the spreading yet additionally boosts its total functionality by ensuring uniformity and precision.
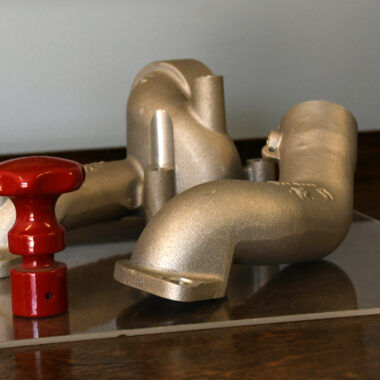
Furthermore, methods like powder layer or painting can be put on light weight aluminum spreadings to provide both aesthetic allure and added protection against ecological variables. By carefully choosing and using the ideal finishing techniques, makers can make certain that their light weight aluminum castings meet the greatest standards of high quality and performance.
Verdict
To conclude, successful aluminum casting requires accuracy and perfection in product choice, mold and mildew layout, procedure optimization, quality control, and finishing techniques. By following best methods in each of these areas, producers can guarantee regular and high-quality cause their light weight aluminum casting procedures. casting aluminum illinois. It is necessary to take notice of every detail and continuously strive for improvement to achieve optimum end results in light weight aluminum spreading
The careful process of aluminum spreading needs focus to information at every stage, from material option to last completing touches.To improve efficiency and quality in light weight aluminum spreading, process optimization plays a pivotal role in maximizing and improving operations result.Process optimization in aluminum spreading not only enhances performance and efficiency but likewise lays the foundation for rigorous high quality control steps to promote market standards.One critical element of quality control in light weight aluminum casting is the usage of advanced screening methods to analyze the stability and residential or commercial properties of the spreadings.In final thought, effective aluminum spreading requires accuracy and perfection in product selection, mold and mildew design, process optimization, quality control, and completing strategies.